Development of pilot scale REX system
(COAT & MGR use cases)
SIMPLI-DEMO has selected two major classes of specialty processes to achieve the specific objectives of the project. In addition to the chemical processes involving suspensions (zeolite and API use cases), the investigated continuous technology of choice is the class of chemical processes involving highly viscous streams with reactive extrusion (REX). The end user COATEX is interested in isocyanate-based polyurethane and polyether synthesis and the end user Megara Resins focuses on non-isocyanate-based polyurethane synthesis.
Many processes can be created more flexible while maintaining the advantages of continuous production by using and further developing continuous flow reactors with adaptable geometry and length and thus residence time and throughput, such as reactive extruders (REX) and continuous oscillating baffle reactors (COBR).
Based on experiences from SIMPLIFY, the EU-funded predecessor project to SIMPLI-DEMO, a modular reactive extrusion system is designed by Fraunhofer (supported by the end users) that provides operational flexibility for a range of polymer synthesis tasks. It can be equipped with modules for the application of microwaves and ultrasound at the most suitable locations along the extruder (with the help of KU Leuven and the National Technical University of Athens). Both the extruder and the screw set-up and processing procedure are designed to allow flexible change between material grades and indicate the superior processability of continuous versus batch system.
Modules related to the upstream and downstream sections are designed and assembled, enabling the continuous self-supporting operation of the reactive extrusion system. The upstream section includes either cyclic batch synthesis of cyclic carbonates or (continuous) pre-polymerization of monomers, allowing to reach sufficient viscosity of reactants/conversion for continuous extrusion processing. For this purpose a reactor is designed and manufactured by Fraunhofer with modular inserts for an energy generator (supported by our partners from MUEGGE and Weber Ultrasonics), spectroscopic probes (supported by TU Dortmund University) and connectors for continuous material feeding and pumping out.
Goals of the two case studies
HEUR reactive extrusion (end user: COATEX)
Structure-forming associative polymers (APs) are increasingly used to control the stability and rheology of dispersions. An important family of commercial APs is the so-called Hydrophobically modified Ethylene oxide URethane (HEUR) thickeners.
Prior work done in SIMPLIFY on HEUR has demonstrated the opportunities of REX with the assistance of ultrasound and microwave technology. The long reaction time needed in the conventional batch process was reduced in REX to less than 10 min, while the product conversion was intact. The use of ultrasound and microwaves in selected REX modules is reducing the overall process time, and therefore also decreasing the length and number of modules in the resulting REX device. With ultrasound and microwaves the yield was doubled compared to the conventional process, and this in a residence time that was ca. 1000 times lower.
SIMPLI-DEMO brings the HEUR synthesis from Technology Readiness Level (TRL) 5 to 7 by introducing modularity and integrating PATs in the pilot device. Flexibility and adaptability is studied by performing HMPE synthesis in the same device.
NIPU synthesis (end user: Megara Resins)
In the synthesis of polyurethane (PU), there is concern over the toxicity of the reactants isocyanate and phosgene (a precursor of isocyanate). Non-isocyanate polyurethanes (NIPUs) are a greener alternative.
In SIMPLI-DEMO, NIPUs are obtained by reacting polycyclic carbonate oligomers with a stoichiometric excess of aliphatic and cycloaliphatic amines containing primary amino groups. The synthesis is carried out with both the classical polymerisation in lab-scale reactors as benchmark and through the reactive extruder.
SIMPLI-DEMO brings NIPU synthesis from below Technology Readiness Level (TRL) 5 to 7 by starting with a parametrization study, followed by transferring the process to a continuous REX with integrated PAT, applying lessons learned in the HEUR case.
End User
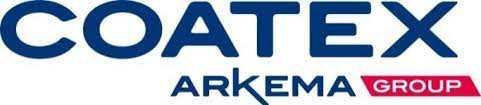
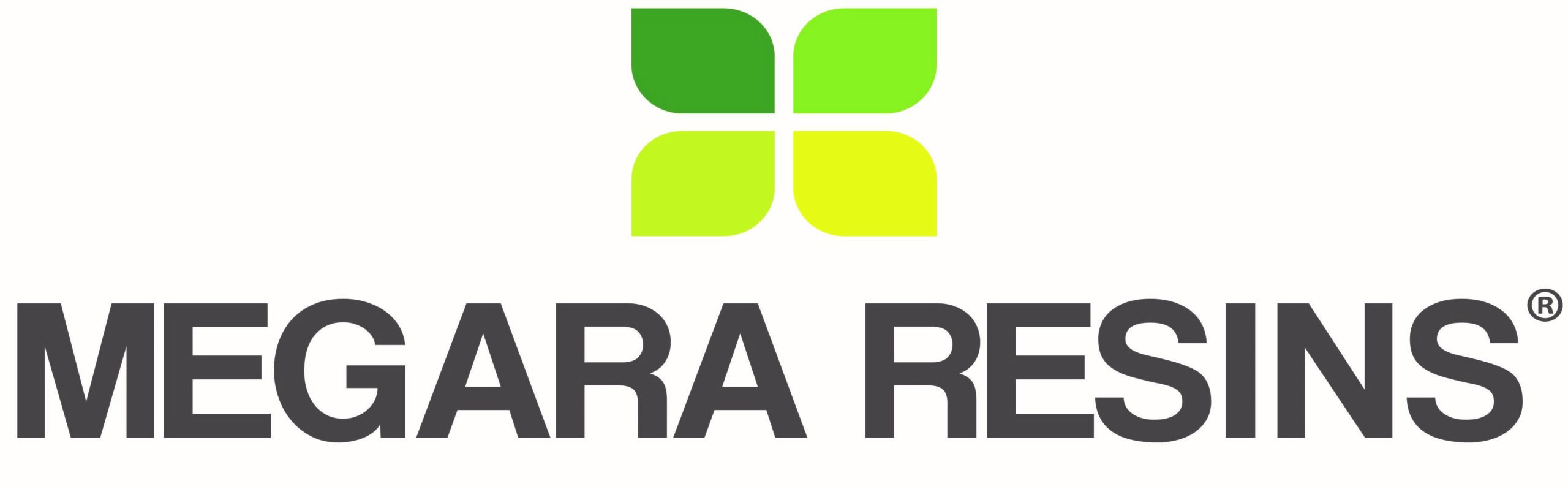